Software
Key features
Composite forming simulation
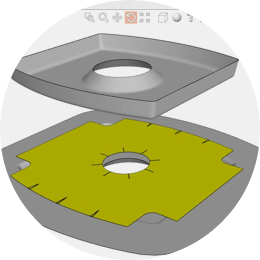
User-friendly model setup
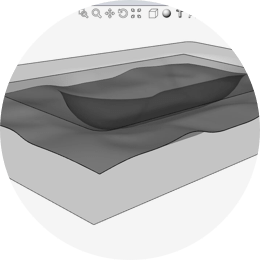
Rigid tooling
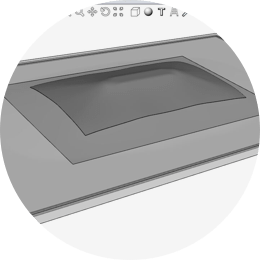
Membrane forming
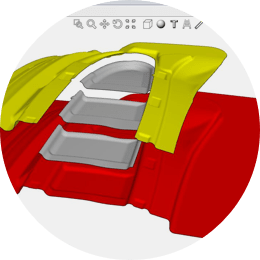
Segmented sequential tooling
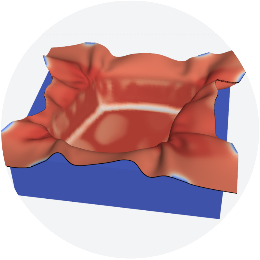
Temperature and crystallinity prediction
Laminate configurations
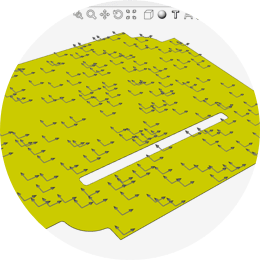
Laminate having any shape
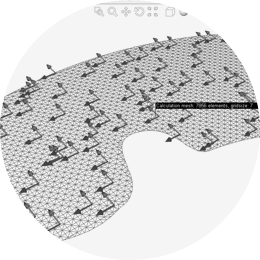
Automatic laminate mesh preconditioner
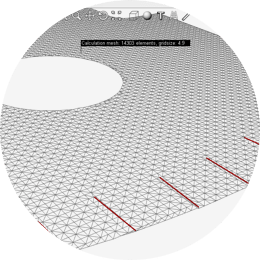
Cuts
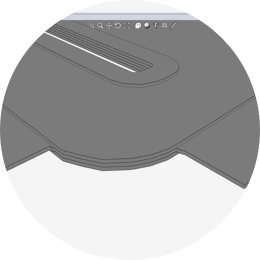
Tailored layups
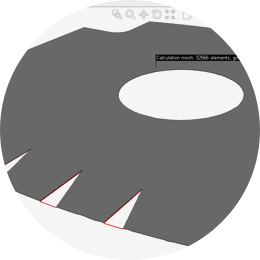
Darts
Handling configurations
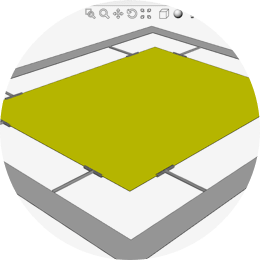
Tensioners
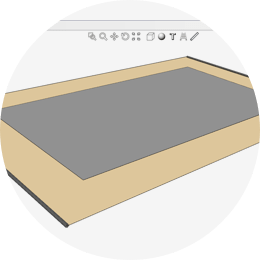
Foil carriers
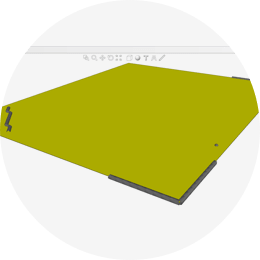
Grippers
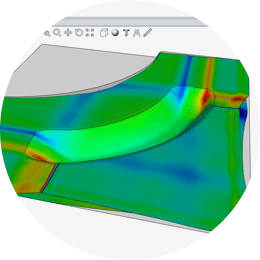
Blank holders
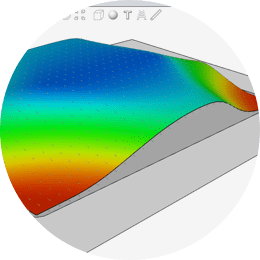
Gravity induced laminate sag
Material behaviour at forming conditions
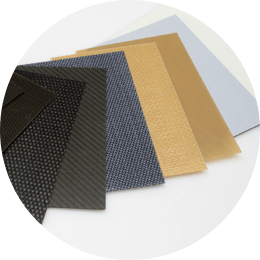
Standard material cards
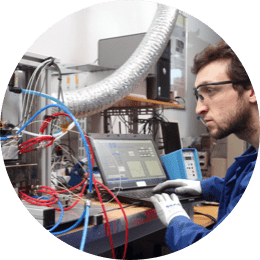
Co-inventor of characterisation methods
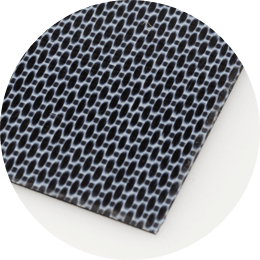
Various composite material types
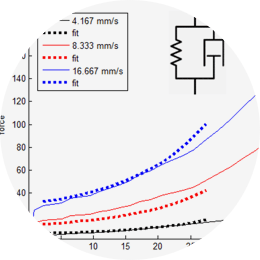
Material models
Data exchange
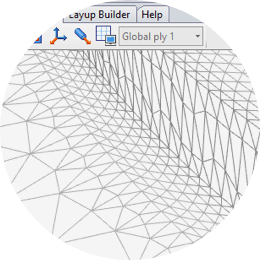
Meshes import
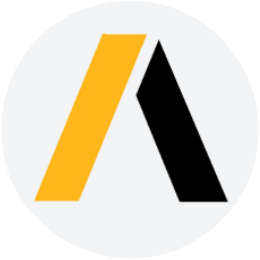
Interface to Ansys Composite PrepPost
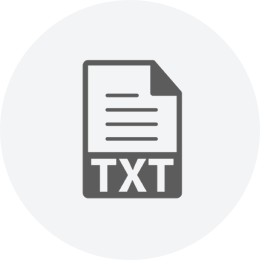
Text file result output
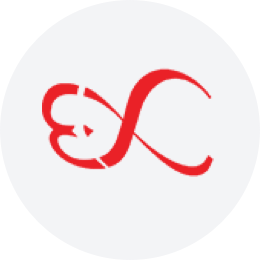
Interface to e-Xstream’s Digimat
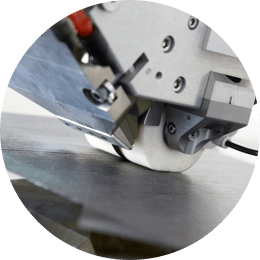
Fibre placement interface
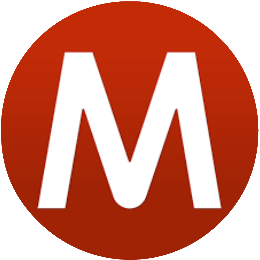
Interface to Moldex3D for flow Analysis
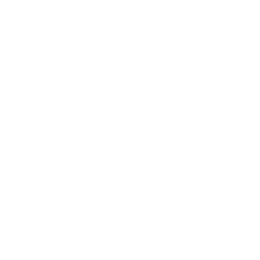
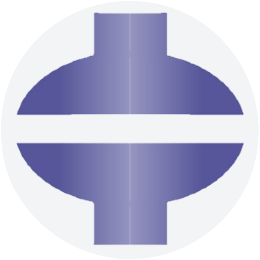
Interface to Abaqus CAE
Solving robustly
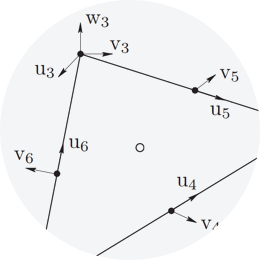
Special shell element
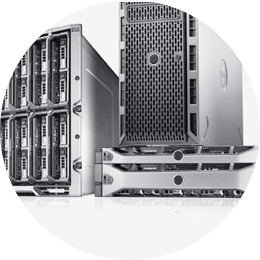
Simulation job scheduling
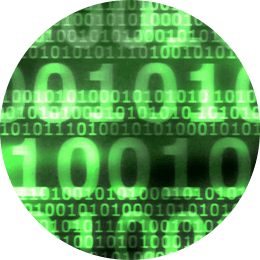
Implicit solver
Realistic predictions
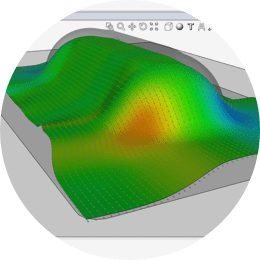
User-friendly analysis
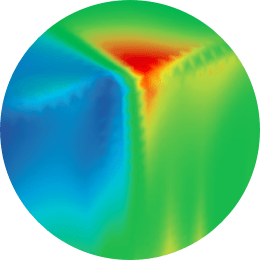
Defect indications
Licence and training
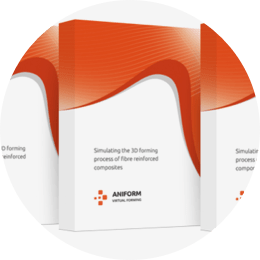
AniForm Software licences
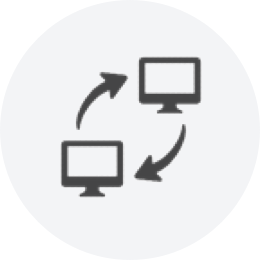
Node-locked and transferrable
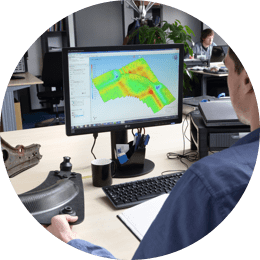